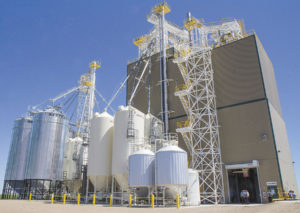
Feed mill already operational two months ahead of schedule
BY KIM LANGEN
The public unveiling of pork company HyLife Ltd.’s brand new $25-million-dollar feed mill in Killarney drew a great crowd on Thursday.
Not only did visitors to the massive Neelin Road project get an excellent stand-up smoked pork loin and ground pork burger lunch, they were also able to take themselves on a self-guided walking tour of six stations, spread out within the multi-level facility, with mill hosts presenting at each point.
“We have food for 500, and it is half gone,” said Kim Pappel, event coordinator, at 1 p.m. on Thursday. “That’s 250 served, and we aren’t finished yet.”
And the mill is already in business making feed – more than two months before the expected completion date.
“We are 63 days ahead of schedule,” said Adolf Doerksen, general manager of the Killarney feed mill. “Over the last few weeks we have milled 2,000 tons of complete feed. That feed has already gone out to local barns.”
Doerksen said that the construction went smoothly because the Killarney mill is a carbon copy of HyLife’s already-existing Randolph, Manitoba mill.
“We used the same guys, and they learned a lot from the Randolph build,” he said.
Station One introduced visitors to the steam generator room, where a sophisticated ‘steam on demand’ system generated some 9,000 pounds of steam per hour using municipal water.
The highly water-efficient system creates steam used expressly in the pelleting process, said Doerksen, and water was recycled, resulting in very little wastewater.
Station Number Two was the control centre of the mill, with some 45 to 50 tons of feed going through each hour, said Russ Schalla, assistant manager of the feed mill. And things would soon get busier, he said.
“Right now we are at not quite two shifts,” said Schalla. “In six weeks we will get to two shifts, and at some point we could get to 24-hour shifts. That would give us maximum use of our equipment. At the end of each eight-hour period we will have three to four hundred tons produced. That’s 15 minutes per ton.”
Station Three was the main production area, where the pellets are made, said Maurice Carriere.
“Steam is added when the pellets go through,” he said. “That makes the pellets move through faster, and it’s more efficient. The steam also helps to pre-cook the pellets, and to break down starches and amino acids, which helps make the food more digestible for the animals. That leads to better feed conversion. We can mix up to 60 different feed rations; usually we do 15 to 20 different rations each day.”
A ‘cyclone’ is used to suck out the air during pellet production, which draws the dust back to the processor, he said. This leads to recapture of the product, and to keeping the place clean, both inside and out of the mill.
At Station Four was Basem Shaker, manufacturing engineer for the highly efficient load-out area.
“It takes 10 minutes from the time the driver pushes the button to be filled up, to when the automated printer prints out a ticket,” said Shaker. “We have 960 tons worth of storage here, with 24 load out bins. A HyLife feed truck has the capacity for 28 tons per truck. We are seeing around 10 trucks per day at present. Our maximum at full production would be 40 to 45 trucks loaded per day.”
At the ‘100 Level’ was Station Five, basically a mixer station for the pellets.
“We keep a sample of run for three months, of everything that goes in or comes out,” said Phil Carriere, manager of the Randolph mill. “We have done 2,000 tons so far, of just sow and finishing hog feed. No nursery feed yet. I’m sure it will start ramping up pretty quick. The pellets come out at 200 degrees Fahrenheit, and here they are cooled to an ambient temperature.”
At Station Six, the scale house, milling assistant Brigitte Rimoncal explained the system.
“We weigh in trucks, using an automatic probe in the truck’s hopper, for farmers delivering grain,” she said. “We test for moisture, for bushel weight, and for vomitoxin. Vomitoxin has to come in at less than, or equal to, one part per million.”
The pork company is currently inviting local farmers to help supply the new mill with grain, they said.
“We are always looking for new suppliers: for corn, wheat, barley, and rye,” said Dennis Kornelsen, director of commodity purchasing for HyLife Ltd. “We want to give local farmers the opportunity to ship locally to us. They can call me on my phone at 204-424-6009, email me at dennis.kornelsen@hylife.com, or text me on my cell at 204-346-3109 to make enquiries.”
ALL SYSTEMS GO AT NEW FEED MILL – Two thousand tons of complete feed has already been processed, pelleted, and shipped out from the new HyLife feed mill in Killarney, well before the expected September start date. HyLife is currently setting up contracts with local farmers to supply grain to the mill, and that feed will eventually be trucked to a number of HyLife hog barns in the area – some of them under construction now.
THE SCALE HOUSE RULES – Milling assistant Brigitte Rimoncal (right) talks with MP Larry Maguire (left) about the state-of-the-art scale house, during the open day held on Thursday at the new HyLife Feed Mill in Killarney. Rimoncal emigrated from the Phillipines in 2016, became a swine technician for HyLife, and later trained for six weeks to become a milling assistant for the new mill, she said.
COLONY INTEREST AT HYLIFE FEED MILL – A cluster of Hutterite brethren were part of the 250 visitors attracted to the HyLife Feed public open house and lunch held on Thursday, July 5, in Killarney. The guys are pictured standing just outside of the scale house and the loading dock of the new feed mill.